The Bowflex SelectTech 560® (ST560) is a “smart” dumbbell, a piece of exercise equipment with embedded sensors and processing to provide training feedback during your workout. The ST560 has an… Read More
WHY YOU NEED A GYRO TO MEASURE POSITION
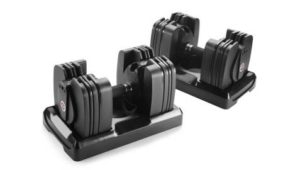
| by Doug Harriman
The Bowflex SelectTech 560® (ST560) is a “smart” dumbbell, a piece of exercise equipment with embedded sensors and processing to provide training feedback during your workout. The ST560 has an… Read More
| by Doug Harriman
Over the last few years, a lot has been written about the future of computing as centered around “big data” algorithms running on servers in data centers. However, embedded systems… Read More
| by Michael Allison
There are typically a number of considerations when choosing whether you want to use a stock gear or to design a custom gear. Two of the key considerations are cost… Read More
| by Doug Harriman
What is a Motion Control System? At the most fundamental level, a motion control system is any system that controls energy flow to generate mechanical motion with some desired properties…. Read More
| by John Pruyn
Mechatronics is not only about the motor, but rather getting the most out of the motors you have. To do that you have to step back and look at the… Read More
| by Bob Callaway
What is the correct (or best) motor to use in a motion control application? Given the myriad choices of type, size and performance it should not be surprising that there… Read More
| by Doug Harriman
In part two of my three-part mechatronics discussion I provided tips for the design of high volume mechatronic systems. In this final entry of the series, I’ll discuss five additional tips… Read More
| by Doug Harriman
As I discussed in part one of my three-part mechatronics discussion, there are many, many types of mechatronics systems in the world. In industry, the largest market segment that would clearly identify… Read More
| by Doug Harriman
The word “mechatronics” was first coined in Japan in the late 1960’s to refer to the synergistic blend of mechanics and electronics. The word has evolved to describe products and… Read More
This phase occurs once the detailed design is complete, and prototypes are built with manufacturing-representative quality and detail. More extensive, formal testing is performed, such as life, reliability, safety, environmental, drop, and vibration.
The design team works closely with the manufacturing team to enable a smooth transfer, often with Simplexity engineers traveling to the contract manufacturer sites to ensure product quality. The design is transferred to the client based upon specific needs, most often after all tests are complete and the design is verified.
Phase 2C iterates on the learnings of Phase 2B and involves a refined prototype build of a fully integrated system. Some projects also benefit from additional iterations of the product based on prior learnings through additional phases (2D, 2E, etc), which are not represented in this graphic. All requirements are intended to be tested, and at the end of Phase 2 there will be confidence that the units will pass verification in Phase 3. The Bill of Materials is further refined, and the team updates estimates for the per unit cost of the product by receiving pricing from vendors and suppliers.
The detailed design phase usually has multiple, iterative sub-phases as the design progresses and representative prototypes are built. Phases 2B and 2C are typically the largest efforts in the product development process, where the specific implementation for all disciplines occurs (mechanical, industrial design, electrical, firmware, systems, software, manufacturing, and quality).
Simplexity typically engages with production component suppliers and contract manufacturing groups early in this phase to provide additional manufacturing input on the design. If the product has stringent testing or certification requirements, pre-screens are performed in this phase prior to formal regulatory agency testing.
The business and user requirements are converted into engineering requirements for the product. The project planning activity is based on the schedule, budget, risk, and initial product requirements. This process is best done as a collaborative team effort with the client, who has the deepest understanding of the market needs and user requirements.
The Simplexity team can be as involved in the production phase as requested by our clients. For clients with internal manufacturing or established relationships with contract manufacturers, our engineers are available to ensure quality is maintained and provide ongoing engineering support as needed.
Simplexity has a dedicated New Product Introduction (NPI) team that can guide the transition from design into production. The NPI team presents multiple options for manufacturing to the client, allowing clients to choose the solution that best suits their needs. This can involve Simplexity performing initial builds in-house prior to full handoff to a contract manufacturer or building the product via established relationships with contract manufacturing partners either domestically or overseas early in the process.
The detailed design phase starts with defining options for the product architecture, with the goal of having the greatest chance of successfully meeting product requirements while best mitigating risk. Engineering activities in this phase include presenting options for hardware components, outlining the system block, sequence, and state diagrams, creating rough CAD, and breadboarding of high-risk subsystems. Results are presented with a description of the pros, cons, and key tradeoffs for each scenario.
Phase 0 is an optional phase for projects where the technical feasibility of the idea has not yet been fully proven. It can consist of research, concept work, exploring initial architecture, performing feasibility studies, and basic prototyping and testing.