“Hey, that’s a great looking application! Where did you find those controls?” Invariably, in the Microsoft .NET community, the answer is found on www.nuget.org. Since the NuGet package management system… Read More
HIGHLIGHTING NUGET PACKAGES INDISPENSABLE FOR MECHATRONICS APPLICATIONS
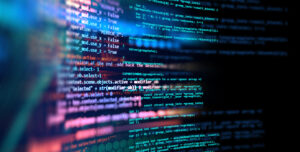